Third-party logistics (3PL)
Grow your 3PL business with the best WMS in the market
of orders ship
same day
lower cost of
picking and
packing
99%
of orders ship
same day
58%
lower cost of
picking and packing
Challenges
A 3PL warehouse management software designed to navigate the industry’s challenges
The 3PL industry faces rising labor costs, retention challenges, and evolving client needs. The pandemic encouraged the move to online shopping, leading to growth in ecommerce and direct-to-consumer (DTC)brands. This shift has introduced new players, increasing pressure on existing 3PL companies to adapt quickly.
Whether you are an emerging player or an established 3PL, there are challenges to overcome
Birth of the hybrid 3PL
The shift in consumer demand continues to push the 3PL industry toward a hybrid model where a single WMS must handle both B2B and B2C needs. Meanwhile, labor shortages and rising costs squeeze profitability and highlight the need for real-time inventory management and more efficient 3PL billing practices.
Solutions
Forward thinking 3PL fulfillment software
Logiwa IO is a modern fulfillment management system (FMS) with features that support both B2B and B2C functionalities—enabling 3PLs to thrive in a hybrid market of online and retail demands. Our comprehensive solution is designed to address the specific pain points faced by 3PLs today.
Logiwa IO’s modern user interface is unmatched in the industry. Easy to use, intuitive screens allow 3PLs to onboard employees faster with minimal need for training. Quickly bring temporary hires up to speed during high-volume peak seasons and cross train employees easily.
Items picked per hour is just one piece of the puzzle. Logiwa IO’s Labor Tracking and Reporting solutions give you comprehensive visibility into all physical and digital activities across your operations, via both desktop and mobile applications. This enables you to benchmark your efficiency against industry standards and easily identify opportunities for improvement. You can also compare performance across different clients, users, and warehouses to gain deeper insights and optimize productivity.
Logiwa IO is built on a headless architecture. This means every action you take on our user interfaces has a matching endpoint (web service) that you can use to design and implement your own experiences beyond Logiwa IO.
Logiwa IO makes it easy to adapt to the needs of the market and new clients. Our no-code drag and drop workflow automation feature lets 3PLs deliver the best service to every client. Create workflows to address every need without the cost associated with custom development or professional services.
Logiwa felt 3PL WMS pricing models begged reassessment. How is it in your WMS provider’s interest to aim for efficiency when their revenue is dependent on the number of user licenses they sell you? That’s why Logiwa IO uses a volume-based pricing model. It aligns your goals with ours. It’s a win-win and another way we help 3PLs fulfill brilliantly.
Customer Success
See what our customers say
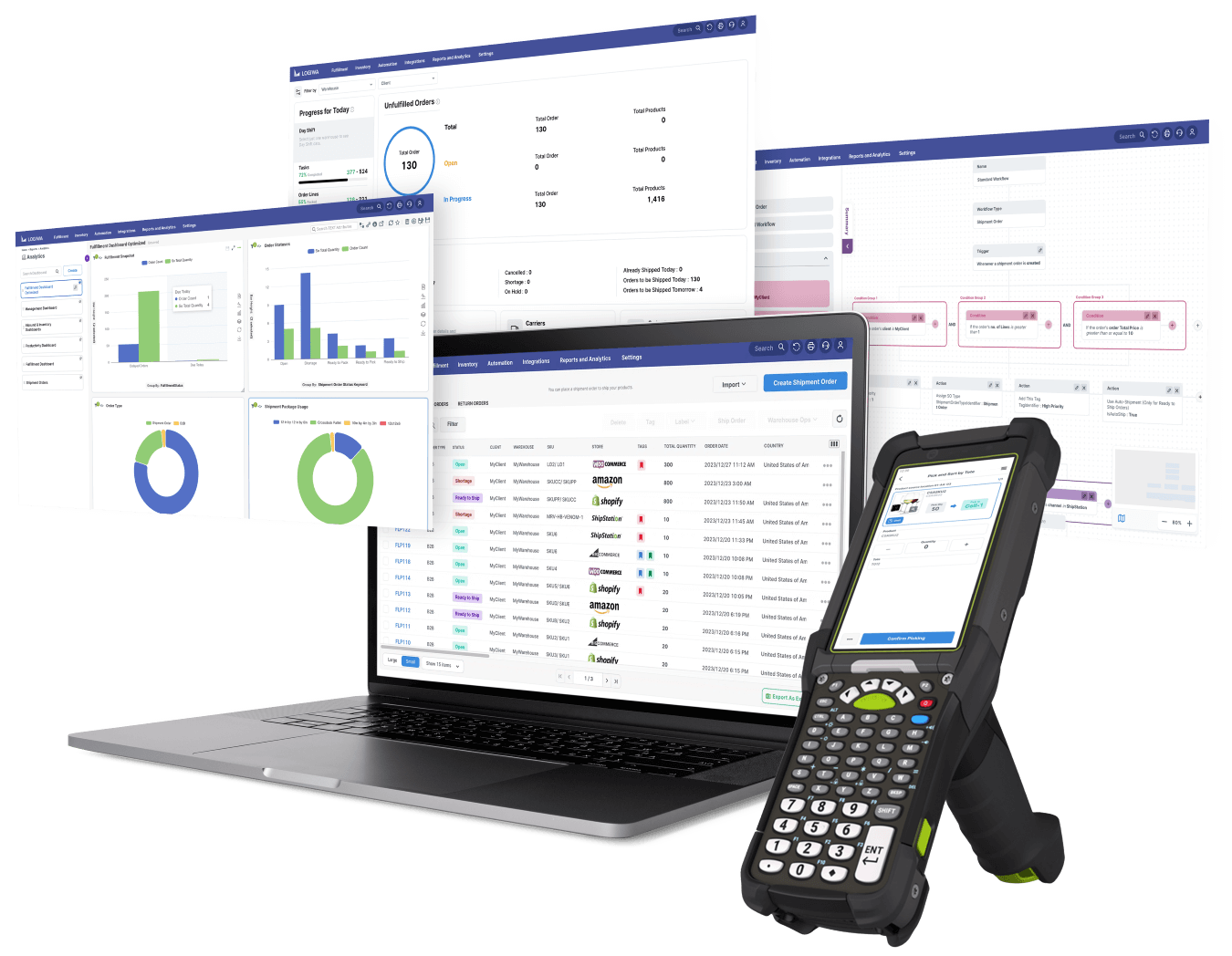