Quickbooks
Quickbooks Inventory Management Cloud Solution
Quickbooks Online Inventory Management Software and Integration
Logiwa’s Cloud Order Fulfillment Platform can help you scale up fulfillment operations, grow your online sales, and manage your bottom line with confidence. With Logiwa, all orders are downloaded automatically from your ecommerce and marketplace channels and the status is updated in Quickbooks automatically as each order moves through your warehouse and shipping process.
Logiwa makes it easy to track inventory across locations, create automated replenishment re-order rules, and keep a tight connection between your purchasing, sales orders, and inventory data.
Logiwa is pre-integrated with Quickbooks for advanced inventory management analysis and optimization. Logiwa is also pre-integrated with NetSuite and SAP accounting systems.
Our state-of-the-art cloud solution makes it easy to centralize all purchasing, sales orders, and inventory data, automate fulfillment operations, optimize order allocation across all your online stores, and analyze your business performance in both Quickbooks and our online reports.
Quickbooks Inventory Management Software Benefits With Logiwa:
Auto-update ASN as sales orders move through your warehouse and shipping process with automated advanced shipping notices sent from Logiwa to Quickbooks
Download your list of products and vendor information from Quickbooks
Keep your stock availability 100% accurate across all your online sales channels and synced with Quickbooks
Gain 100% control across your supply chain with safety stock and shortage notifications
Route your orders automatically across your locations with our smart “Order Routing Algorithm”
Speed up fulfillment and shipping with smart batches that group orders for the fastest pick-and-pack operations
Save even more time with smart picking algorithms and mobile scanning functionality
Manage kits/bundles with ease – Logiwa calculates the bundle quantity based on components available and syncs availability in real-time
Find the best rate with our “Rate Shopping” algorithms
Lower costs and speed up shipping with auto-printed labels and packing lists included in our “Batch Printing” functionality
Update shipment status in Quickbooks automatically for faster revenue recognition
Send billing statements for each client directly to your 3PL Quickbooks account
Avoid out of stocks and make smart re-order decisions with our advanced reports and full visibility inside Quickbooks inventory management
Manage returns efficiently
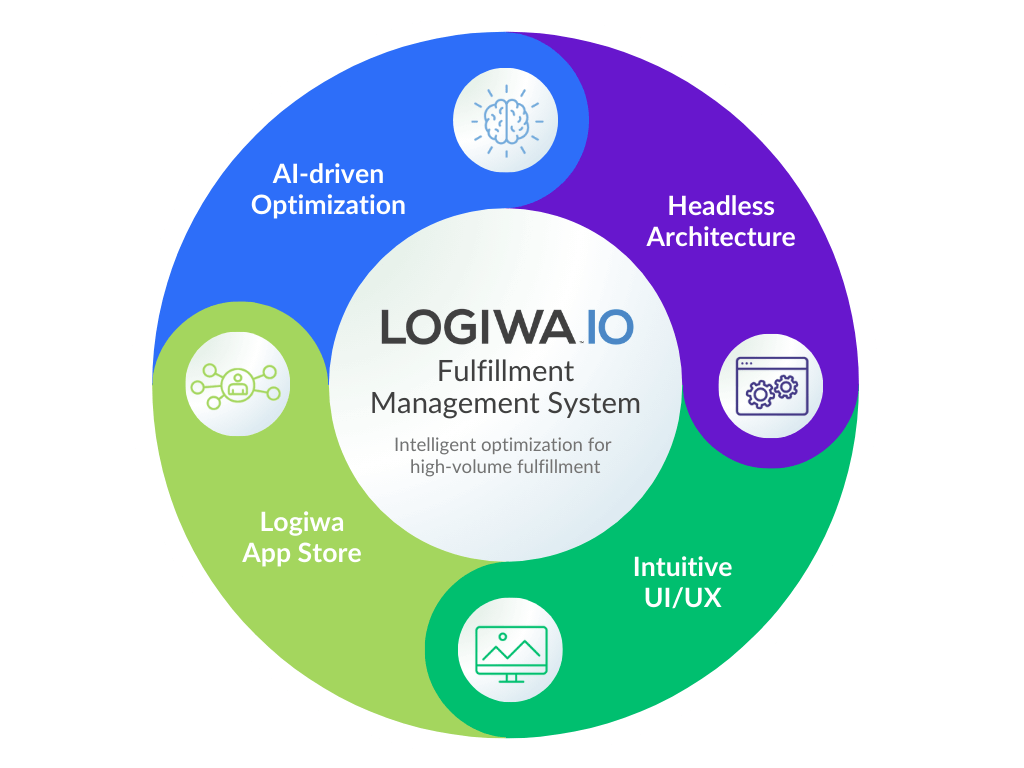
Our Quickbooks Inventory Management solution is part of the Logiwa Cloud Fulfillment Platform built specifically for high-volume B2C and DTC businesses
The Logiwa Cloud Fulfillment Platform is a fully integrated WMS and order fulfillment system that empowers companies to run a fulfillment experience and grow your direct-to-consumer business – without additional headcount.
AI-driven Optimization
Streamline operations with waves and jobs for enhanced outbound flow. Monitor on-ground activities to optimize workforce management with labor standards.
Headless Architecture
Groundbreaking headless, versionless, and serverless architecture. Seamlessly adapt your operations to changing needs, design your own add-ons, and scale effortlessly.
Intuitive UI/UX
Ensures an engaging user experience with an intuitive app design. Onboard new employees in hours, not days.
Logiwa Marketplace
Our partner ecosystem allows you to add features and modules—your own, and those from the marketplace—for limitless configurability and continuous innovation.
Logiwa IO is the flexible fulfillment management system with integrations for every business.
Logiwa Makes a Fast Impact on Your Business
100%System Uptime
FAQs about Quickbooks Inventory Management Cloud Solution
What is Quickbooks Inventory Management software?
How does the Quickbooks Inventory Management software work?
Why do I need a Quickbooks Inventory Management software?
How to do multi-channel inventory management?
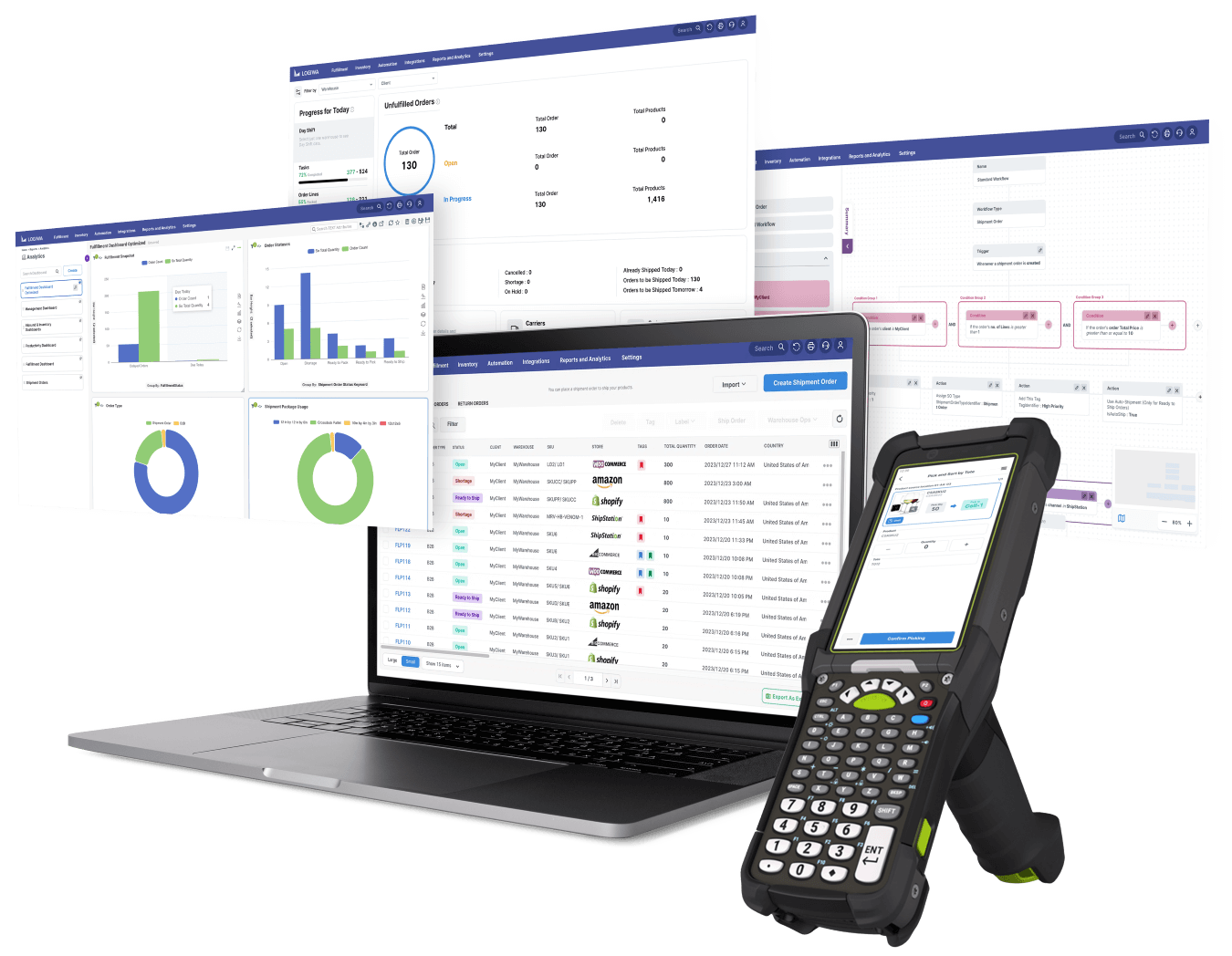