Optimize your operations to maximize productivity
Logiwa is warehouse management software done right. Our WMS helps brands, online sellers and 3PLs achieve high-volume order success.
Why Choose Logiwa WMS as Your Warehouse Inventory Management Software?
Logiwa WMS allows you to run a fully digital warehouse. Our cloud-based warehouse inventory management system offers a wide array of benefits and features at your fingertips – including mobile apps, smart job batching, automation rules, real-time exception handling, and online reports. Our forward-thinking approach to order fulfillment and industry-leading customer support has made us the number one choice for today’s competitive warehouse operations.
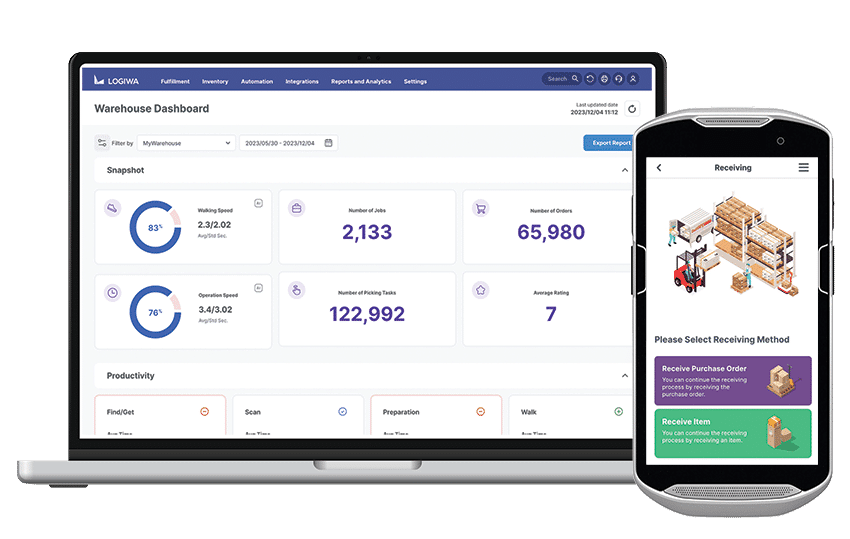
Let us show you Logiwa IO
The benefits of Logiwa’s warehouse management software
Improved Inventory Accuracy and Visibility
Real-time Tracking and Reporting
Streamlined Order Fulfillment Process
Enhanced Warehouse Efficiency and Productivity
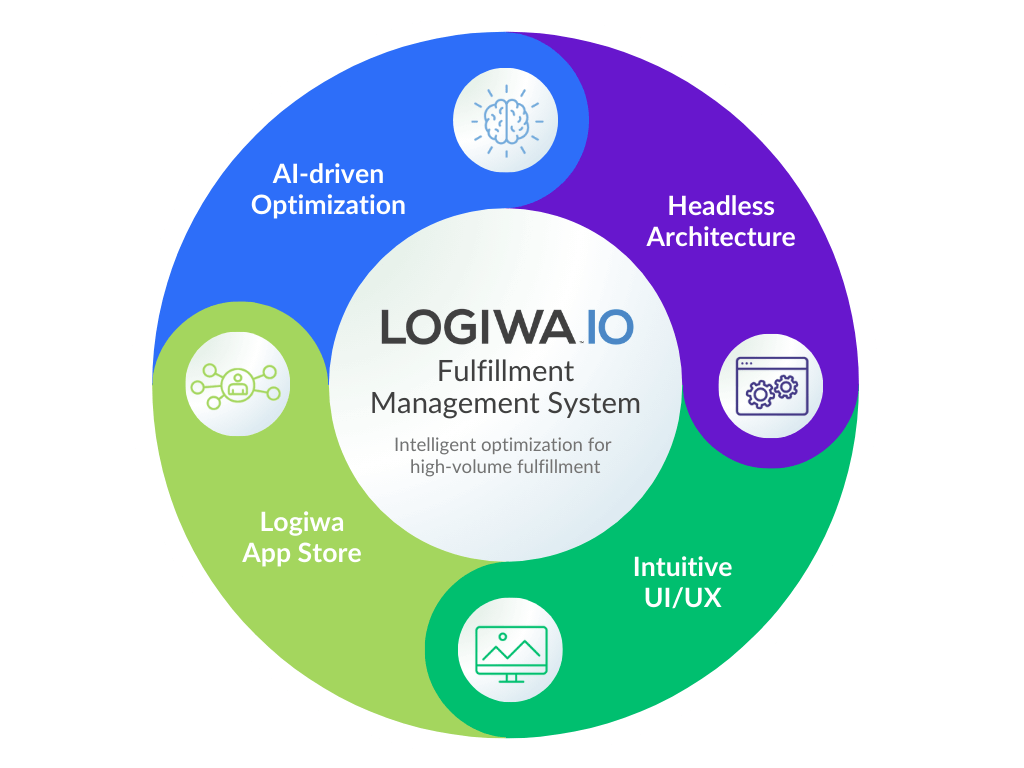
Logiwa’s Cloud Warehouse Management Software is Built Specifically for High-volume B2C and DTC businesses
The Logiwa Cloud Fulfillment Platform is a fully integrated order fulfillment system that empowers companies to run a digital fulfillment experience and grow direct-to-consumer business—without additional headcount.
The key features of Logiwa IO
Advanced inventory management for multi-warehouse operations
The control you need
Optimize multi-warehouse operations at both the macro and micro levels. Logiwa’s Warehouse Management System gives you the controls you need to:
- optimize inventory levels across fulfillment centers with location-based rules,
- perfect inventory management within each distribution center with
- group and zone-based rules,
- fixed and dynamic picking locations, and
- clear location capacities.
Get real-time visibility into inventory shortages at each warehouse, route orders to the best fulfillment center, and manage inventory transfers with ease.
Mobile Order Tracking and Fulfillment
Real-time information on any device
Mobilize everything to understand how your employees move and operate in your distribution center. Mobile scanners send information about every item being received, put away, picked, packed, shipped, counted and transferred directly into Logiwa Cloud WMS System. Mobile reports let everyone see real-time inventory, order progress, and jobs from any mobile device.
Integration with Leading Ecommerce Platforms
Synced for optimized inventory
Sync your warehouse operations directly with the orders coming in through online channels such as Shopify, Magento, or Amazon. Keep inventory optimized during fluctuations in demand with real-time updates, and achieve 100% order accuracy with step-by-step mobile guidance as pickers pick, scan, report discrepancies, and adjust effortlessly as exceptions arise.
Barcode Scanning and Labeling
Streamlined processes
Simplify your warehouse processes with barcode scanning and labeling. Logiwa WMS supports barcode scanning for receiving, picking, packing, and shipping, eliminating manual errors and improving overall efficiency.
Customer Success
See what our customers say
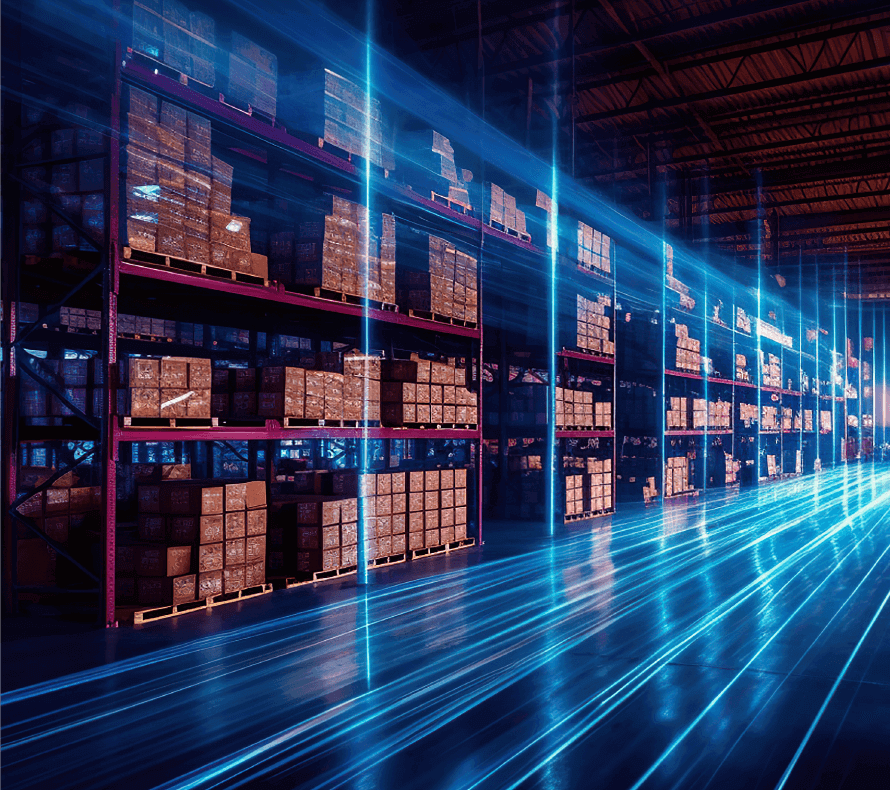
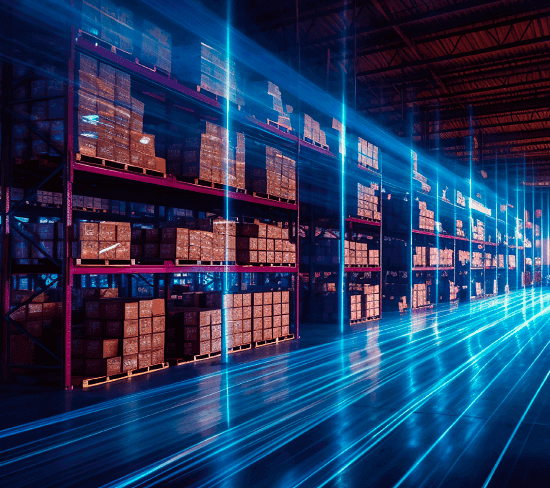
More than just great software
We’re a high-volume Fulfillment Success Company.
As a true SaaS product, Logiwa WMS continually adds new features and innovations to drive your business forward. We solve your most pressing fulfillment challenges and help you meet the toughest industry standards.
Implemented in weeks,
not months
Logiwa IO is a true Cloud system that is easy to deploy, configure, and update as your business scales.
Optimized using AI
and automation
Our pre-built automation rules and AI powered jobs speed up everything from your inbound operations to your picking, packing and shipping processes.
Supported every step of
the way
Our customers rave about our customer support and we pride ourselves in our 7-9 minutes response time. We’re more than your software provider – we’re your partner for success.
Implemented in weeks, not months
Logiwa IO is a true Cloud system that is easy to deploy, configure, and update as your business scales.
Optimized using AI and automation
Our pre-built automation rules and AI powered jobs speed up everything from your inbound operations to your picking, packing and shipping processes.
Supported every step of the way
Our customers rave about our customer support and we pride ourselves in our 7-9 minutes response time. We’re more than your software provider – we’re your partner for success.
Pre-integrated with the leading ecommerce, marketplace, shipping, robotics, and accounting platforms.
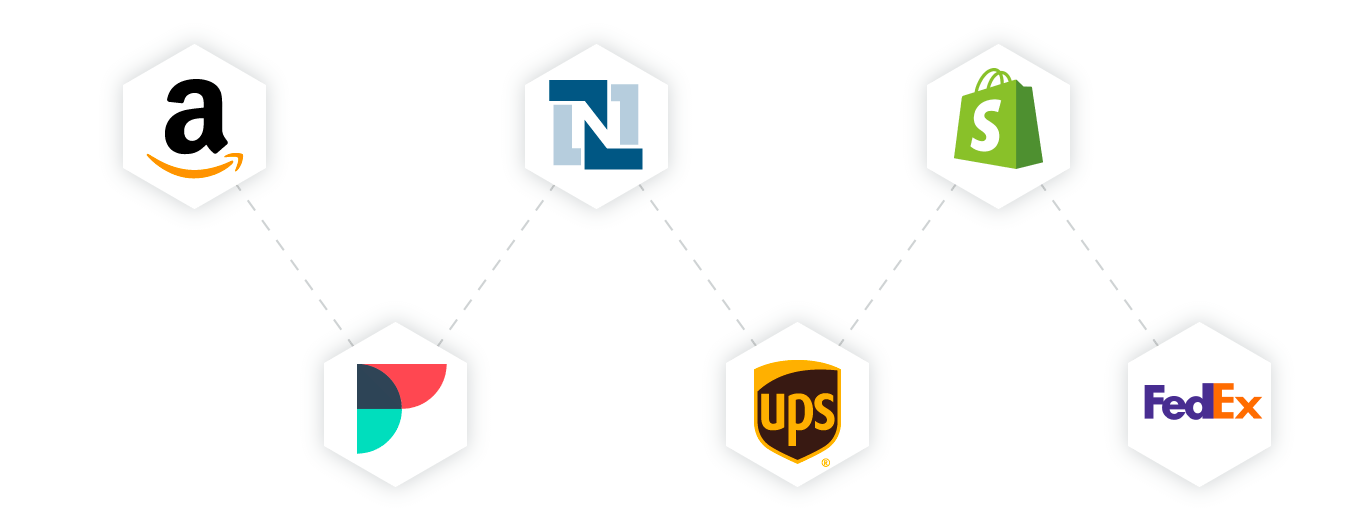
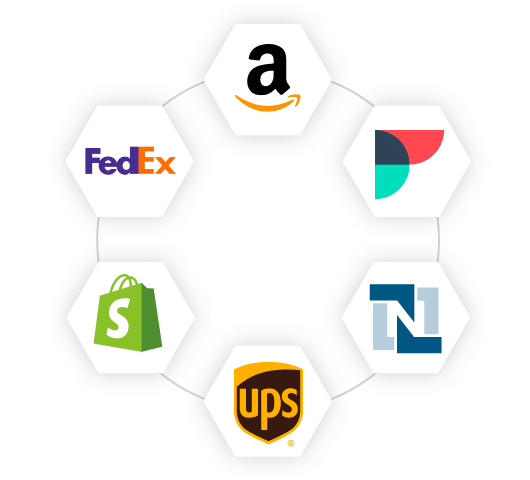
Our areas of expertise
Logiwa’s warehouse inventory management system has everything brands and online sellers need to achive high-volume order fulfillment success
Warehouse
Operations
Warehouse
Productivity
Warehouse
Optimization
FAQs about warehouse management software
What is a warehouse management system (WMS)?
A WMS solution from Logiwa can help to improve the efficiency and accuracy of warehouse operations, leading to reduced costs and increased productivity. Logiwa WMS can also help to reduce the risk of errors, such as lost or damaged goods, and improve customer satisfaction by enabling faster and more accurate order fulfillment.
How is a WMS different from an enterprise resource planning (ERP) system?
An ERP system is a broader type of business management software that includes a range of modules for managing different aspects of your business, such as accounting, HR, and supply chain management. A WMS is focused specifically on managing warehouse operations and is typically integrated with an ERP system as one of its modules.
How is Logiwa WMS implemented in my warehouse?
Implementing Logiwa WMS involves four distinct phases to address the unique needs of your operation, such as its size and complex fulfillment processes. Our highly effective approach includes business process & change analysis, configurations testing, training & practices, a dry run, assisted go-live care, and follow-up support for a positive post-onboarding experience. We utilize project management tools, so that it is clear who is responsible for what tasks to keep the project on track and even, whenever possible, complete your first order with you.
How does Logiwa WMS work?
Logiwa WMS consists of a central database that stores information about the warehouse and its operations, as well as a user interface that allows warehouse staff to access and update this information and 3PL operations can provide clients with custom portals. The system may also include mobile devices, such as handheld scanners, that allow warehouse staff to track and manage inventory in real-time.
Can Logiwa WMS be customized to meet the specific needs of my business?
Yes, Logiwa WMS is highly configurable and can be tailored to meet the specific needs of your business. This can include customizing the user interface, integrating with other business systems, and adding or modifying fulfillment features to meet your specific requirements.
How does Logiwa WMS benefit my business?
A WMS solution from Logiwa can help to improve the efficiency and accuracy of warehouse operations, leading to reduced costs and increased productivity. Logiwa WMS can also help to reduce the risk of errors, such as lost or damaged goods, and improve customer satisfaction by enabling faster and more accurate order fulfillment.
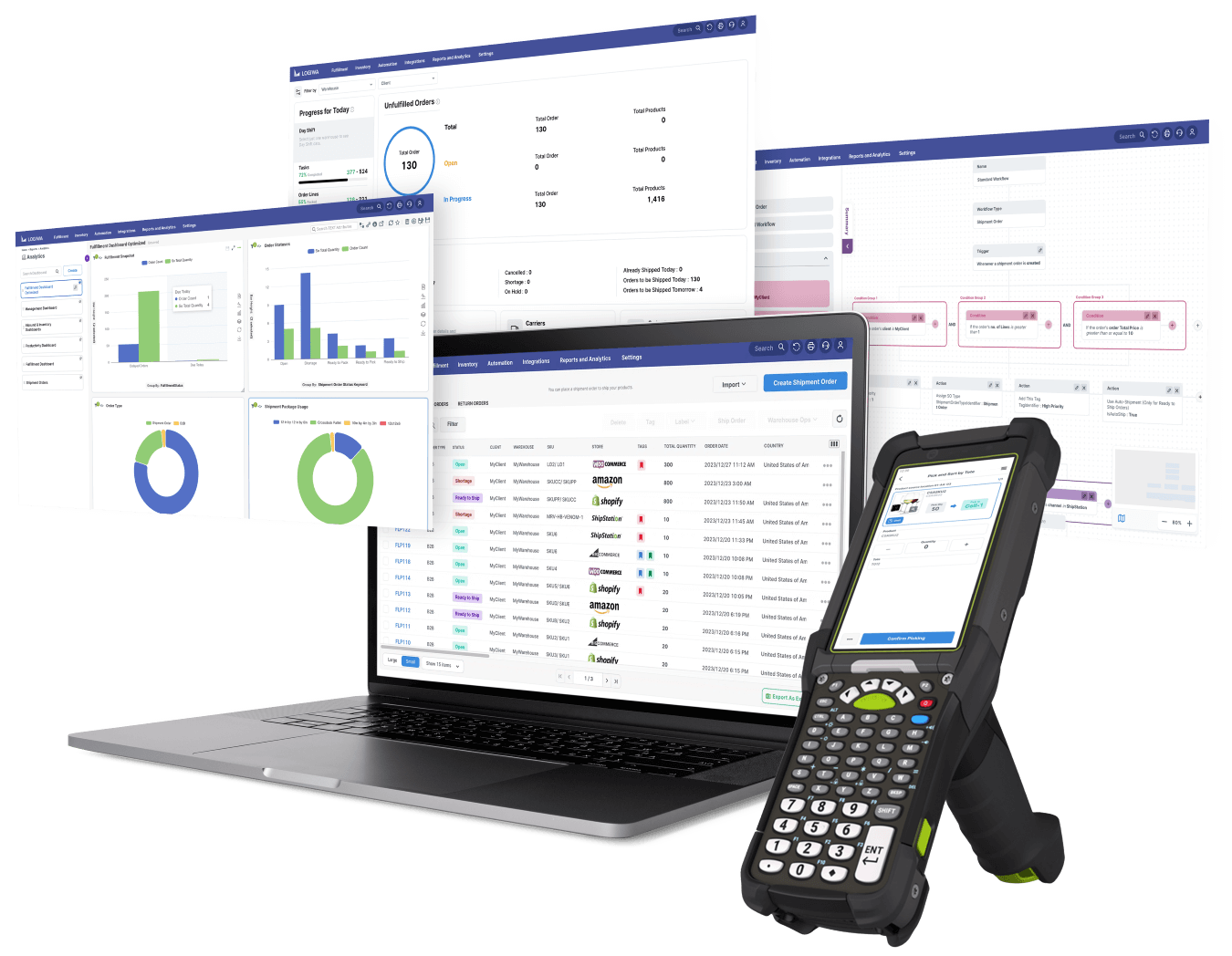