Advanced AI warehouse technology is pushing the limits of what is possible for B2B and DTC operations. As a result, fulfillment standards are tougher than ever.
The logistics revolution aims for perfect order fulfillment, which means delivering orders flawlessly, on time, and without errors. But reaching perfection is difficult, especially given the complexities of supply chain management and order fulfillment.
Enter AI technology, a game-changer for warehouses seeking to optimize efficiency and meet customer expectations. This blog explores the pivotal role AI warehouse technology plays in achieving perfect order fulfillment.
Contents
- The Challenge of Achieving Perfect Order Fulfillment
- The Role of AI in Transforming Warehouse Operations
- AI-Driven Order Fulfillment: The Basics
- Advanced AI Warehouse Technology for Enhancing Order Accuracy
- Measuring the Impact of AI: Calculate Perfect Order Rate
- Overcoming Challenges in Implementing AI Warehouse Solutions
- FAQs Related to Perfect Order Fulfillment
Key Takeaways
- The ability to deliver accurate, on time, and perfect orders is crucial in today’s consumer-driven market.
- AI-driven order fulfillment utilizes advanced technologies to streamline warehouse operations and enhance order accuracy (e.g. AI jobs, computer vision, robotics, etc.).
- From demand forecasting to automated picking systems, AI plays a crucial role in optimizing fulfillment processes and ensuring customer satisfaction.
- Thorough planning, training, and selection of scalable AI solutions are essential to future-proofing warehouse operations and maximizing the benefits of AI technology.
The Challenge of Achieving Perfect Order Fulfillment
Perfect order fulfillment is defined as the process of delivering orders without any errors, on time, and in perfect condition. And these days, it is the only standard consumers are willing to accept.
In fact, it’s been reported that 65% of consumers say they will cease shopping with a retailer after 2-3 late deliveries, and 81% will stop after 2-3 incorrect deliveries.
Despite its importance, achieving a high fulfillment accuracy rate is challenging due to the complexities of warehouse operations, including inventory management, picking, packing, and shipping. Errors in these processes significantly impact customer satisfaction and brand reputation.
Unfortunately, common fulfillment challenges, including mis-picks, stockouts, and shipping errors have caused the industry average for fulfillment accuracy rates, to remain below expectations. These challenges underscore the need for innovative solutions to improve order fulfillment processes.
Watch the video above to see the how Logiwa IO handles B2B fulfillment.
The Role of AI in Transforming Warehouse Operations
AI technology is revolutionizing warehouse operations by automating and optimizing tasks that traditionally required manual intervention. From inventory management to shipping, AI-driven solutions are making warehouses smarter and more efficient.
By leveraging different forms of AI warehouse technology, perfect order fulfillment is not just a futuristic dream but a present-day reality. It’s all thanks to AI-driven automation, analytics, and robotics.
Related Content: AI and Robotics: The Dynamic Duo for High-Efficiency Fulfillment
AI-Driven Order Fulfillment: The Basics
AI-driven order fulfillment powers advanced technologies to streamline warehouse operations and improve order accuracy. Here are the three common examples:
- Machine learning algorithms analyze historical data to predict stock levels and manage reordering, minimizing the risks of overstock and stockouts.
- Robotics technology automates warehouse processes, significantly reducing human error and increasing the speed of workflows.
- Smart analytics offer valuable insights into customer behavior and order patterns, enabling more accurate forecasting and inventory management.
These are just a few of the basic ways AI is being used to help operations achieve perfect order fulfillment. Let’s take a look at some more advanced types of AI technology, as well as some ways to measure its effects on your business.
Advanced AI Warehouse Technology for Enhancing Order Accuracy
AI Powered Jobs
AI job optimization is an aspect of modern warehouse solutions like Logiwa IO. It focuses on using operational data (e.g. order details, stock levels, shipping details, locations, etc.) to direct packing operations. This strategically structures jobs to eliminate delays and human error.
- AI Jobs typically visit 40% fewer locations when combining Picking & Packing to optimize.
- Logiwa IO users have experienced up to 58% efficiency gain with AI-driven jobs.
AI job optimization ensures the right products are picked and packed efficiently, and directly contributes to the fulfillment accuracy rate.
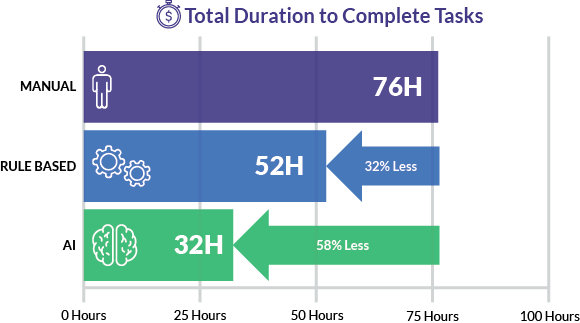
Unlock a personalized tour of Logiwa IO
Automated Picking Systems
Robotic picking systems are renowned for their precision and speed, and they drastically reduce errors in the picking process. Automated picking systems (e.g. robotic arms equipped with sensors and cameras) can identify and pick items from storage shelves with pinpoint accuracy. These robots are programmed to follow predefined paths and algorithms, ensuring that the correct items are selected for each order.
This type of AI represents a cornerstone of warehouse technology, offering tangible benefits like reduced labor costs and faster, more accurate order fulfillment.
Intelligent Inventory Management
AI algorithms play a crucial role in predicting stock levels and managing reordering processes. Intelligent inventory management helps in reducing overstock and preventing stockouts, ensuring that warehouses can fulfill orders promptly and accurately.
These algorithms analyze historical sales data, current inventory levels, seasonal trends, and other relevant factors to accurately predict future demand for products. By leveraging machine learning techniques, these algorithms continuously learn and adapt to changing market conditions. As a result, inventory levels are optimized and accurate to meet customer demand.
Advanced Sorting and Packing Solutions
AI systems and algorithms sort and pack orders to meet customer needs and reduce mistakes in the fulfillment process. These systems use computer vision to scan and identify items, ensuring the correct products are processed.
AI-powered sorting and packing solutions help warehouses handle various product types and sizes efficiently. These systems group similar items for easier packing by categorizing them based on characteristics like size, weight, and fragility. This reduces packing time and lowers the chance of mistakes and damage during shipping.
Computer Vision
As previously mentioned, computer vision technology enables computers to interpret and understand visual information from images or video footage. Warehouses use computer vision systems for object recognition, quality control, and automated inspection. For example, computer vision algorithms can identify products on conveyor belts, verify their integrity, and flag any defects or anomalies in real-time.
Computer vision ensures that only high-quality items are shipped to customers. Additionally, computer vision algorithms can analyze data collected from multiple sources, such as cameras and sensors, to provide comprehensive insights. This allows operations to make continuous improvements that safeguard order accuracy.
Autonomous Vehicles and Drones for Material Handling
The use of autonomous vehicles and drones within warehouses marks a significant advancement in material handling. These technologies improve operational precision and contribute to a higher fulfillment accuracy rate by ensuring that goods move quickly and safely through the warehouse.
By leveraging autonomous vehicles and drones, warehouses can streamline the movement of goods with unparalleled efficiency, ensuring that items are transported to their designated locations without exception. This optimized workflow minimizes the risk of errors and delays in order processing, ultimately promoting perfect order fulfillment.
Real-time Data Analysis and Forecasting
Real-time data analysis and forecasting are critical for achieving fast and accurate order fulfillment. AI processes real-time data to make informed decisions, helping warehouses to stay ahead of demand, manage inventory more effectively, and root out inefficiencies affecting order processing and fulfillment results.
Through the utilization of AI-driven algorithms, warehouses are able to analyze vast streams of real-time data with precision. This promotes proactive decision-making and strategic planning. This ability to process data in real-time empowers warehouses to not only meet but maintain competitive fulfillment standards.
Related Content: Precision Order Picking: How Online Retailers Can Avoid Mis-picks
Measuring the Impact of AI: Calculate Perfect Order Rate
To evaluate AI’s effectiveness in order fulfillment, businesses must consider specific metrics and KPIs. The rate of returns from picking errors, order fulfillment time, and customer satisfaction rates are key. For quick snapshots into the health of your operations, you should also track Perfect Order Rate (POR) and On-Time Delivery (OTD).
Warehouses implementing AI technology witness a significant improvement in perfect order rate (POR) and on-time deliveries, underscoring the value of AI in achieving perfect order fulfillment. AI may start with forecasting and optimized inventory management, but it leads to smoother fulfillment operations and more successful fulfillment logistics.
Overcoming Challenges in Implementing AI Warehouse Solutions
Adopting AI for order fulfillment comes with its set of challenges, including the initial investment in technology, the need for staff training, and the integration of AI systems with existing warehouse management systems. However, by adopting a strategic approach, you can overcome these obstacles and quickly reap the benefits of AI.
The primary challenge in adopting AI for order fulfillment is the upfront investment required for implementing it. You may need to allocate resources for purchasing hardware, software licenses, and hiring specialized personnel to develop or integrate AI systems. The integration of AI systems with existing warehouse management systems can pose technical challenges, such as compatibility issues and data migration concerns.
However, you can mitigate risks and maximize returns by adopting a strategic approach to AI implementation. Training programs can be designed to familiarize employees with AI systems and processes, ensuring that they can effectively utilize these tools to enhance order fulfillment operations. Continuous training and upskilling initiatives will also help your business keep pace with evolving technologies and industry best practices.
Thorough planning, continuous training, and choosing scalable AI solutions promote success no matter what stage you’re at in your AI journey. By prioritizing scalable AI solutions that can adapt to changing requirements and scale with business growth, you can future-proof your operations and maintain a competitive edge in the market.
AI-Driven Fulfillment Management Systems (FMS)
The transformative potential of AI in achieving perfect order fulfillment cannot be overstated. As you strive to meet the growing number of customer orders, embracing AI technology offers a path to enhancing operational efficiency, accuracy, and increasing customer satisfaction.
Logiwa IO helps operations take order fulfillment to the next level with our AI-driven FMS. Our solution has helped users achieve:
- 38% increase in productivity
- 58% improved task efficiency
- 93% orders shipped in 24 hours
Investing in AI warehouse technology is not just about staying competitive; it’s about redefining what’s possible in the realm of order fulfillment. Learn more in our blog, “AI-Driven Fulfillment with Logiwa IO.”
FAQs Related to Perfect Order Fulfillment
What is perfect order fulfillment? What is the impact of AI in order fulfillment?
Perfect order fulfillment is the percentage of orders that arrive on time and without errors, according to their promised delivery date. It refers to the process of delivering orders accurately, on time, and in perfect condition, without any errors or damages. Achieving perfect order fulfillment has become a key industry standard and a differentiator that sets fulfillment operations apart.
How does AI warehouse technology support order accuracy?
AI warehouse technology supports order accuracy by automating and optimizing various warehouse operations, including inventory management, picking, packing, and shipping, thereby reducing the likelihood of errors. By minimizing manual intervention and optimizing workflows, AI enhances order accuracy and efficiency, ultimately improving customer satisfaction.
How do you calculate fulfillment accuracy rate?
The fulfillment accuracy rate is calculated by dividing the number of orders correctly fulfilled by the total number of orders fulfilled, then multiplying by 100 to get a percentage. This essential metric enables businesses to gauge the effectiveness and consistency of their order fulfillment processes, guiding them in optimizing operations for greater accuracy and efficiency.
How does AI technology contribute to correct invoicing and supply chain metrics?
AI enhances the success rate of perfect order fulfillment. It enables businesses to generate correct invoices based on accurate order information and monitor supply chain metrics such as order accuracy, fulfillment speed, and items ordered on time. Through AI-driven insights, companies can identify areas for improvement, streamline processes, and ultimately achieve perfect order fulfillment.
Fast-paced order fulfillment with customer satisfaction at the forefront
Warehouse Management
Modern digital WMS powers a modern fulfillment experience