As today's ecommerce-driven order fulfillment market evolves, merchants need a warehouse management system (WMS) that...
High-volume Order Fulfillment Blog
Cutting-edge industry trends and practical tips to make fulfillment excellence a competitive advantage
Featured Blog
Experience Brilliant B2B Fulfillment with Logiwa IO
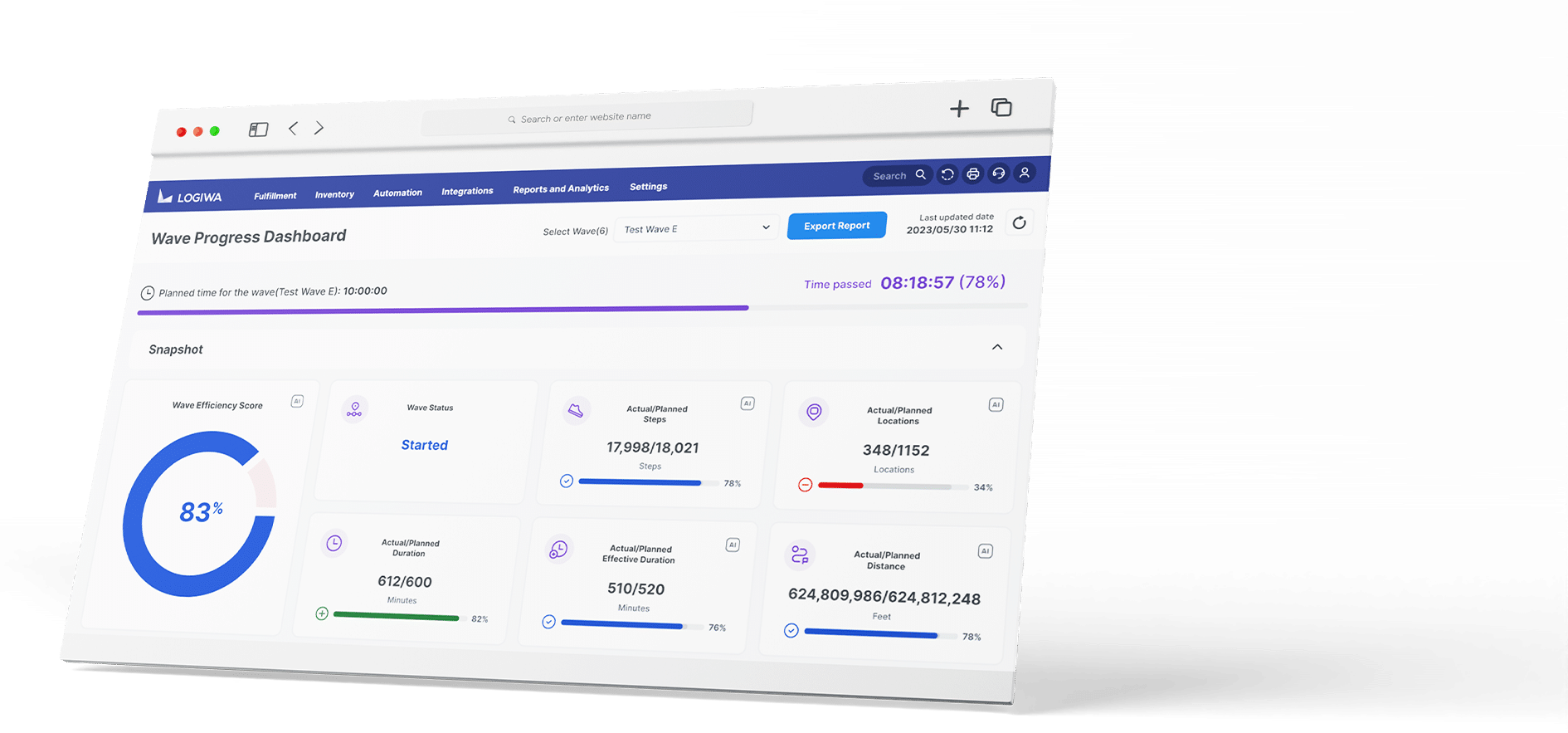
Boosting fulfillment speed and inventory accuracy with a modern warehouse management system (WMS)
Between evolving ecommerce complexities, shifting global policies that strain the supply chain, and ever-increasing...
Reducing picker travel time: Enhancing warehouse efficiency with automation and smart slotting
In modern fulfillment centers, reducing pickers' walking distance is pivotal for enhancing efficiency and...
Future-proof your operations with the CTO’s playbook for smart warehouse technologies
The global retail ecommerce sales reached around $6 trillion in 2024, with a 31% growth forecast for the coming years....
How AI and IoT are transforming warehouse management in enterprise supply chains
Many enterprise warehouses struggle with outdated technology, fragmented data, and manual workflows that slow...
5 transformative technologies redefining warehouse management operations in 2025
The modern, high-volume logistics environment has made warehouse management more than just a back-end operation....
Enhancing customer satisfaction with automated order management systems
Statistics indicate that ecommerce accounted for over 17% of retail sales globally in 2024. By 2029, this figure is...
How cloud-based WMS is redefining logistics for 3PL providers
Logistics is undergoing a fundamental transformation. The popularity of direct-to-consumer (DTC) fulfillment models...
A guide to improving profits with inventory management software
Profit margins are under pressure due to rising labor costs and unpredictable supply chains. For fulfillment centers,...
Top 3PL software solutions for high-volume fulfillment centers 2025
High-volume fulfillment operations are under increasing pressure due to the explosive growth of ecommerce. In 2025,...
How cloud WMS enables real-time fulfillment visibility in the supply chain
Many supply chain businesses, including third-party logistics companies (3PLs) and direct-to-consumer brands, now...
How advanced warehouse management systems minimize fulfillment errors
The current supply chain environment is faster and more complex than ever, which means fulfillment accuracy is...